I’ve been chased for more info about the build of our boat, so apologies for being slow – here’s an update and photos from earlier in the year when we visited!
(Also see Travels section post)
Back in February the composite work was largely complete; the hulls had been post-cured and faired and the interior structure was about 90% done. The topsides are beautiful and quite curved, so represent a time-consuming element of the build process and we agreed, last year, for Julian to take moulds from the topsides of our boat in order to improve the time-efficiency of this part of future CM46 builds. This, of course, delayed our boat but I guess I have plenty of empathy with the whole productionising, scaling-up and boat-building process, so was a soft touch when he asked.
Having been unable to visit South Africa until early this year due to travel restrictions, the timing of our trip actually proved perfect to give us a great feel for the boat, the layout and spaces above and below decks.
Have to say, we were blown away by the quality of the composite work and the overall look and feel of the boat. Aesthetics are subjective but we think the boat already looks AMAZING and will only get better when finished and fitted. The spaces feel plenty big enough – actually bigger than we’d expected or remembered from our original visit when we looked at the shell of 46 #1. Maybe some areas will appear to shrink a little after fit-out when tables, doors and other items are installed but we were very happy (and a little relieved) with the saloon and cockpit layout that we helped develop – especially as it’s now the standard layout. It’s much easier to envisage it all when standing on the boat than it was locked-down in our home loft office, with a lap-top screen, paper, rule and calculator!
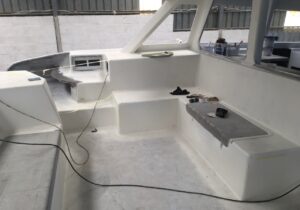
While at Current Marine we finalised many remaining details with Julian and the CM team – from deck layout elements such as exact helm seat and winch locations to suit our reach, right down to our planned usage of lockers and resulting desired internal shelf spacing, etc, etc. Our mates will be amused (but not surprised) to hear we specifically went to a liquor store to check the average height of a rum bottle.
The furniture is all foam cored composite, fully laminated into the hull before being faired and finally painted. It contributes to the structure, is super-light and won’t creak. Locker doors are also foam cored composite panels and they were away at the veneer specialist, being laminated with our chosen oak finish.
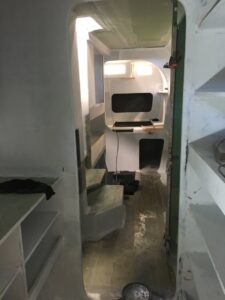
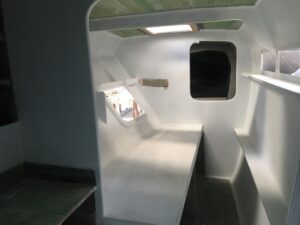
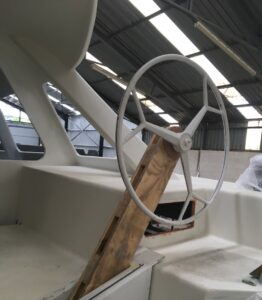
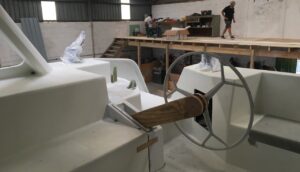
The last couple of years have been a challenging and full-on period for Current Marine. In addition to the obstacles presented by Covid they have also literally worked around their factory being doubled in size to accommodate more boats in build. Construction was in the latter stages while we were there and, unexplainably gratifyingly, even the factory builder proudly told us he’d shipped a 36’ steel hull from France and was fitting it out at home before heading off cruising in a few years time! The CM team has grown significantly, now including a mix of experienced people who’ve worked with Julian for years and new members coming from other high-level production backgrounds.
Electronics and electrical systems will be installed by Clarence Hendricks of CYS, based in Cape Town, and we were able to spend an afternoon on the boat with Clarence and his son looking at everything from nav station layout and MFD locations, to domestic 220v socket positions. Clarence is also widely experienced – cruising his own boat and racing offshore as bowman (flippin’ handy for any skipper to find a bowman who happens to be an electronics expert as well!) around the South Atlantic and in Asia. Clarence has now also liaised with Sertec (the CMCE lightining protection manufacturer) and Ocean Data Systems (the UpSideUp manufacturer) before installing those systems.
Julian introduced us to the cushions supplier, located just up the road from CM in Knysna so we could talk through our design preferences and we created a spreadsheet to document it all once home. Our steadfastly simple boat needs thirty separate bed and seat cushions… and that’s before we get to scatter cushions…!
Final stop, before flying home, was to meet David Rae at North Sails in Cape Town to discuss all the options. I’ll create a separate blog post about our sails and set-up.
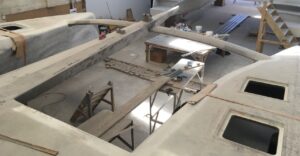
After much analysis, we’ve decided to use Coppercoat antifouling and, as it’s British made, I bought it direct. Provided it is applied correctly (it’s epoxy based so will be straightforward for CM) and well-finished by flatting back to smooth it and activate (expose) the copper, it should be effective. Coppercoat’s particular benefit is that it lasts for years so the annual, expensive antifoul application chore is eliminated. An added major bonus on our boat will be that the skinny, shallow hulls mean we’ll be able to easily wipe them from the dinghy or when swimming to minimise the hassle and cost of lifting out. The ability to regularly clean the boat, without the angst of rubbing off soft antifoul paint (hastening the need for re-coating), will be great. Coppercoat is more expensive but the lifespan and reduced haul out costs should more than compensate.
We’ve shipped the Coppercoat to South Africa with loads of other equipment for the boat. From egg cups up to Derek the dinghy and everything in between, we loaded a 20’ container in the farmyard next to home last week and it’s now en-route to Cape Town. We’ve worked with PSP Freight in the UK to organise the freight and Pronto Clearing will handle the import in Cape Town. There is a load of empty space in the container but it allowed us to use all the equipment we already own and was the most cost efficient option.

As I write this, the composite work on the boat has fundamentally been completed (I guess there will always be something to add or change until we actually sail away), the interior has been painted and equipment is being dry-fitted before removal for a final finishing paint coat. The exterior of the hull has been primed and will shortly be sprayed with Awlgrip top coat. We’ve chosen to have many of the ancillary composite components (davits, bimini pillars, stanchions, pedestals, table legs etc) in satin black to match the spars, longeron and forward beam and these are soon to be finished in a specialist local spray-booth.
We enjoyed our time in SA in February so much that we’re tempted to head over again before the boat is finished – the excuse being it would be great to see the various systems during installation and have the best possible understanding of them once we’re off cruising. We’d love to take the chance to travel around some other places over there and a wine expert, TV and newspaper critic friend from home has promised to set-up one or two vineyard visits with her contacts. We’re not at all sophisticated on that front and had better brush up our knowledge first – so an Aslina Chardonnay from the Western Cape is chilling at the moment!